In today’s highly competitive business environment, having a robust and efficient supply chain is paramount to success. A well-managed supply chain can lead to increased profitability, enhanced customer satisfaction, and a strong competitive advantage. Enterprise Resource Planning (ERP) systems are playing an increasingly crucial role in streamlining supply chain operations and maximizing efficiency. This article delves into the key functionalities of ERP systems and explores how they contribute to a seamless and optimized supply chain.
Understanding the Supply Chain Management Process
Supply chain management (SCM) is the process of planning, implementing, and controlling the flow of goods and services from the point of origin to the point of consumption. It involves coordinating all the activities that transform raw materials into finished products and deliver them to the end customer. SCM encompasses a wide range of activities, including procurement, production, inventory management, warehousing, transportation, and customer service.
Key Components of Supply Chain Management
A well-functioning supply chain relies on several essential components:
- Suppliers: These are the businesses that provide raw materials, components, and other inputs to the supply chain.
- Manufacturers: They transform raw materials into finished products.
- Distributors: They move goods from manufacturers to retailers and other customers.
- Retailers: They sell finished products to consumers.
- Customers: The end users of the goods and services produced by the supply chain.
Benefits of Effective Supply Chain Management
Implementing effective SCM strategies can bring numerous benefits to businesses:
- Reduced Costs: Optimizing inventory levels, transportation routes, and production processes can lead to significant cost savings.
- Improved Efficiency: Streamlined operations and better coordination across the supply chain result in increased efficiency and productivity.
- Enhanced Customer Satisfaction: Timely deliveries, accurate orders, and responsive customer service contribute to higher customer satisfaction levels.
- Increased Profitability: By reducing costs and improving efficiency, SCM can boost a company’s overall profitability.
- Improved Risk Management: Proactive planning and mitigation strategies can help minimize the impact of potential disruptions and supply chain risks.
Challenges in Supply Chain Management
Despite its benefits, SCM also presents several challenges:
- Global Complexity: Supply chains are increasingly global, making coordination and communication more complex.
- Disruptions: Natural disasters, economic downturns, and geopolitical events can disrupt supply chains.
- Technological Advancements: Rapidly evolving technologies, such as automation and e-commerce, require businesses to adapt and innovate.
- Sustainability: Companies are facing growing pressure to operate sustainably, which includes minimizing environmental impact and promoting ethical practices within their supply chains.
Conclusion
Supply chain management is a crucial aspect of modern business operations. By understanding the key components, benefits, and challenges of SCM, businesses can develop effective strategies to optimize their supply chains, reduce costs, improve efficiency, and enhance customer satisfaction.
How ERP Systems Improve Supply Chain Visibility
In today’s fast-paced and interconnected world, businesses are constantly seeking ways to optimize their operations and gain a competitive edge. One crucial aspect of achieving this goal is enhancing supply chain visibility. This refers to the ability to track and monitor the flow of goods and information throughout the entire supply chain, from raw materials to finished products.
ERP systems play a pivotal role in improving supply chain visibility by integrating various business processes and data into a single platform. By centralizing information, ERP systems provide a comprehensive view of the supply chain, enabling businesses to:
- Track inventory levels in real-time: ERP systems allow businesses to monitor inventory levels at various locations, including warehouses, distribution centers, and retail stores. This real-time data provides insights into stock availability, potential shortages, and opportunities for optimization.
- Monitor supplier performance: ERP systems can track supplier delivery times, quality metrics, and overall performance. This information enables businesses to identify potential risks and proactively manage supplier relationships.
- Analyze demand patterns: By integrating data from sales, marketing, and customer service systems, ERP systems can provide insights into demand patterns and trends. This information allows businesses to forecast demand accurately and adjust production and procurement plans accordingly.
- Identify bottlenecks and inefficiencies: ERP systems can analyze data from across the supply chain to identify bottlenecks and areas for improvement. This allows businesses to optimize processes, reduce lead times, and improve overall efficiency.
By providing real-time data and insights, ERP systems empower businesses to make informed decisions, reduce risks, and optimize their supply chain operations. This enhanced visibility translates into numerous benefits, including:
- Improved customer satisfaction: With accurate information on product availability and delivery times, businesses can provide better service to their customers.
- Reduced costs: By optimizing inventory levels, minimizing waste, and streamlining processes, businesses can significantly reduce costs throughout the supply chain.
- Enhanced agility and responsiveness: ERP systems enable businesses to adapt quickly to changing market conditions and customer demands.
- Increased profitability: By improving efficiency, reducing costs, and enhancing customer satisfaction, ERP systems contribute to increased profitability for businesses.
In conclusion, ERP systems are essential tools for enhancing supply chain visibility and driving operational excellence. By providing real-time data and insights, ERP systems empower businesses to make informed decisions, optimize processes, and gain a competitive edge in today’s dynamic marketplace.
Inventory Management and Optimization
In the realm of business operations, inventory management stands as a pivotal function, encompassing the processes of planning, controlling, and optimizing the flow of goods from procurement to delivery. Effective inventory management plays a crucial role in ensuring the smooth operation of a business, minimizing costs, and maximizing customer satisfaction.
Inventory optimization, a key component of inventory management, involves utilizing data-driven techniques and strategies to determine the optimal levels of inventory to hold, thereby striking a balance between meeting demand and minimizing holding costs. By optimizing inventory levels, businesses can reduce the risk of stockouts, eliminate excess inventory, and enhance overall profitability.
Benefits of Effective Inventory Management:
- Reduced Costs: Optimal inventory levels minimize storage and handling costs, reduce waste from obsolescence, and optimize transportation expenses.
- Improved Customer Satisfaction: Timely delivery of goods, stemming from adequate inventory levels, enhances customer satisfaction and loyalty.
- Enhanced Operational Efficiency: Effective inventory management streamlines operations, reduces lead times, and enables businesses to respond swiftly to market fluctuations.
- Increased Profitability: Minimizing inventory holding costs, maximizing sales opportunities, and reducing the risk of stockouts contribute to improved profitability.
Key Components of Inventory Management:
- Demand Forecasting: Accurately predicting future demand is crucial for effective inventory planning.
- Inventory Control: Establishing systems for tracking inventory levels, monitoring stock movements, and managing stock replenishment.
- Inventory Optimization: Implementing strategies to determine optimal inventory levels, minimizing holding costs, and reducing the risk of stockouts.
- Inventory Turnover: Measuring the rate at which inventory is sold and replaced, indicating the efficiency of inventory management.
- Inventory Valuation: Determining the monetary value of inventory, which is essential for financial reporting and decision-making.
Strategies for Optimizing Inventory:
- Just-in-Time (JIT) Inventory: A production and inventory management strategy that aims to receive goods just as they are needed, minimizing inventory holding costs.
- Materials Requirements Planning (MRP): A planning and control system that uses a computer to determine the amount of materials needed for production.
- Enterprise Resource Planning (ERP): A suite of software applications that integrates various business processes, including inventory management.
- Data Analytics: Leveraging data analytics tools to gain insights into inventory patterns, demand trends, and potential disruptions.
In conclusion, effective inventory management is an essential aspect of business success. By optimizing inventory levels, businesses can minimize costs, improve customer satisfaction, enhance operational efficiency, and increase profitability. Through the implementation of appropriate strategies and technologies, organizations can achieve optimal inventory management and gain a competitive advantage in today’s dynamic marketplace.
Demand Forecasting and Planning
Demand forecasting and planning are crucial aspects of any business, especially those involved in manufacturing, retail, and service industries. Effective demand forecasting enables organizations to predict future customer demand for their products or services, allowing them to make informed decisions regarding production, inventory, pricing, marketing, and sales strategies.
Demand forecasting involves using historical data, market trends, and other relevant factors to estimate future demand. It is a critical process that helps businesses understand the anticipated needs of their customers and adjust their operations accordingly. Accurate demand forecasting can significantly contribute to:
- Reduced inventory costs: By predicting demand accurately, businesses can optimize their inventory levels, minimizing overstocking and stockouts.
- Improved production planning: Forecasting helps manufacturers schedule production runs effectively, ensuring timely delivery and reducing lead times.
- Enhanced marketing and sales strategies: Understanding future demand patterns allows businesses to target their marketing campaigns and sales efforts more effectively.
- Optimized pricing strategies: Based on demand forecasts, businesses can adjust pricing strategies to maximize revenue and profitability.
Demand planning, on the other hand, involves converting demand forecasts into actionable plans. It encompasses various activities such as:
- Sales and operations planning (S&OP): Aligning demand forecasts with production capacity, inventory levels, and financial resources.
- Supply chain management: Coordinating with suppliers to ensure timely procurement and delivery of raw materials and components.
- Capacity planning: Assessing and adjusting production capacity to meet projected demand.
- Inventory management: Establishing optimal inventory levels and implementing strategies for replenishment.
The success of demand forecasting and planning depends on the accuracy of the forecasts and the effectiveness of the planning process. Several factors influence the accuracy of forecasts, including the availability of historical data, the complexity of the business environment, and the chosen forecasting methods. Organizations should leverage advanced forecasting techniques and tools, such as statistical models, machine learning algorithms, and collaborative forecasting platforms, to enhance the accuracy of their forecasts.
Furthermore, effective communication and collaboration between departments involved in demand planning, including sales, marketing, operations, and finance, are crucial for successful implementation. By integrating forecasting and planning processes, organizations can achieve better demand management, optimize their operations, and enhance their overall performance.
Procurement and Supplier Management
Procurement and supplier management are critical aspects of any successful business. They involve the processes of acquiring goods and services from external sources, managing relationships with suppliers, and ensuring that the company receives the best possible value for its money.
Effective procurement and supplier management can deliver significant benefits, including:
- Reduced costs: By negotiating favorable prices and terms with suppliers, businesses can save money on their purchases.
- Improved quality: Working with reputable suppliers can help businesses to ensure that they receive high-quality goods and services.
- Increased efficiency: Streamlined procurement processes can reduce the time and effort required to purchase goods and services.
- Enhanced risk management: By carefully selecting and managing suppliers, businesses can mitigate risks related to supply chain disruptions, product defects, and other issues.
- Improved sustainability: By partnering with suppliers who share their commitment to sustainability, businesses can reduce their environmental impact and improve their social responsibility.
There are many different approaches to procurement and supplier management, but some common principles include:
- Strategic sourcing: Identifying the most appropriate suppliers for each need, considering factors such as price, quality, delivery time, and sustainability.
- Supplier relationship management: Building strong relationships with suppliers based on trust, communication, and collaboration.
- Performance monitoring: Tracking supplier performance and identifying areas for improvement.
- Risk assessment and mitigation: Proactively identifying and addressing potential risks in the supply chain.
- Continuous improvement: Continuously looking for ways to optimize procurement processes and enhance supplier relationships.
In today’s competitive business environment, effective procurement and supplier management are essential for success. By implementing best practices and leveraging technology, businesses can optimize their supply chains, reduce costs, improve quality, and gain a competitive edge.
Production Planning and Scheduling
Production planning and scheduling are critical components of any manufacturing or service organization. They involve the process of determining what to produce, how much to produce, and when to produce it. Effective production planning and scheduling ensure that products are manufactured on time, within budget, and meet customer requirements.
Key Aspects of Production Planning and Scheduling
The key aspects of production planning and scheduling include:
- Demand Forecasting: Accurately predicting future demand for products is essential for effective production planning. This involves analyzing historical sales data, market trends, and other relevant factors.
- Capacity Planning: Ensuring that the production process has the necessary capacity to meet forecasted demand is crucial. This involves assessing available resources, such as equipment, labor, and materials, and identifying potential bottlenecks.
- Master Production Schedule (MPS): The MPS outlines the production plan for a specific period, specifying the quantities of each product to be produced and the delivery dates. It serves as the basis for detailed scheduling.
- Material Requirements Planning (MRP): MRP calculates the exact quantities of materials needed for each product, ensuring timely procurement and avoiding shortages or excess inventory. It also helps optimize inventory levels.
- Production Scheduling: This involves creating a detailed schedule that specifies the sequence of operations, the time allocated to each operation, and the resources required. It ensures that production runs smoothly and meets deadlines.
- Production Control: This involves monitoring and controlling the production process to ensure that it adheres to the schedule and meets quality standards. It also includes tracking production progress, managing inventory, and identifying and addressing any deviations.
Benefits of Effective Production Planning and Scheduling
Effective production planning and scheduling offer numerous benefits, including:
- Improved efficiency and productivity: Optimized scheduling minimizes downtime and maximizes resource utilization, resulting in increased output and reduced costs.
- Reduced lead times and improved customer satisfaction: Meeting delivery deadlines consistently enhances customer satisfaction and builds trust.
- Lower inventory levels and reduced costs: Accurate forecasting and efficient scheduling minimize excess inventory, reducing storage costs and waste.
- Enhanced quality control: A well-defined schedule ensures that products are manufactured to meet quality standards, minimizing defects and rework.
- Improved communication and collaboration: Production planning and scheduling require collaboration among various departments, fostering communication and coordination.
Conclusion
Production planning and scheduling are vital for any organization that produces goods or services. By implementing effective planning and scheduling strategies, companies can optimize their operations, enhance efficiency, reduce costs, and deliver products on time and to the required standards. With the continuous evolution of technologies such as Enterprise Resource Planning (ERP) systems and advanced analytics, production planning and scheduling are becoming more sophisticated, offering even greater opportunities for optimization and improved business performance.
Order Fulfillment and Logistics
Order fulfillment is the process of receiving, processing, and shipping orders to customers. It is a critical part of any business that sells products online or in-store. Effective order fulfillment can help businesses increase customer satisfaction, reduce costs, and improve their overall efficiency.
Logistics is the management of the flow of goods and services from the point of origin to the point of consumption. It involves a number of activities, including transportation, warehousing, inventory management, and customer service. Logistics is essential for businesses of all sizes, but it is especially important for companies that operate on a global scale.
Key Components of Order Fulfillment and Logistics
There are a number of key components to order fulfillment and logistics, including:
- Order processing: This includes receiving orders, verifying customer information, and processing payments.
- Inventory management: This involves tracking inventory levels, managing stock, and ensuring that products are available when needed.
- Packaging and shipping: This includes selecting the appropriate packaging materials, packing orders, and shipping them to customers.
- Customer service: This involves providing support to customers throughout the order fulfillment process, from order placement to delivery.
Benefits of Effective Order Fulfillment and Logistics
Effective order fulfillment and logistics can provide a number of benefits to businesses, including:
- Increased customer satisfaction: Customers are more likely to be satisfied when they receive their orders on time and in good condition.
- Reduced costs: Efficient order fulfillment and logistics can help businesses reduce costs associated with transportation, warehousing, and inventory management.
- Improved efficiency: Effective order fulfillment and logistics can help businesses streamline their operations and improve their overall efficiency.
- Competitive advantage: Businesses that have strong order fulfillment and logistics capabilities can gain a competitive advantage in the marketplace.
Tips for Improving Order Fulfillment and Logistics
There are a number of things that businesses can do to improve their order fulfillment and logistics processes. Some tips include:
- Invest in technology: There are a number of technologies available that can help businesses automate and optimize their order fulfillment and logistics processes.
- Optimize your warehouse layout: A well-designed warehouse layout can help to improve efficiency and reduce costs.
- Partner with reliable logistics providers: Choosing the right logistics provider can be crucial for success.
- Provide excellent customer service: Customers are more likely to be loyal to businesses that provide excellent customer service.
By following these tips, businesses can improve their order fulfillment and logistics processes and gain a number of benefits. Effective order fulfillment and logistics are essential for success in today’s competitive marketplace.
Benefits of Integrating ERP with Supply Chain Management
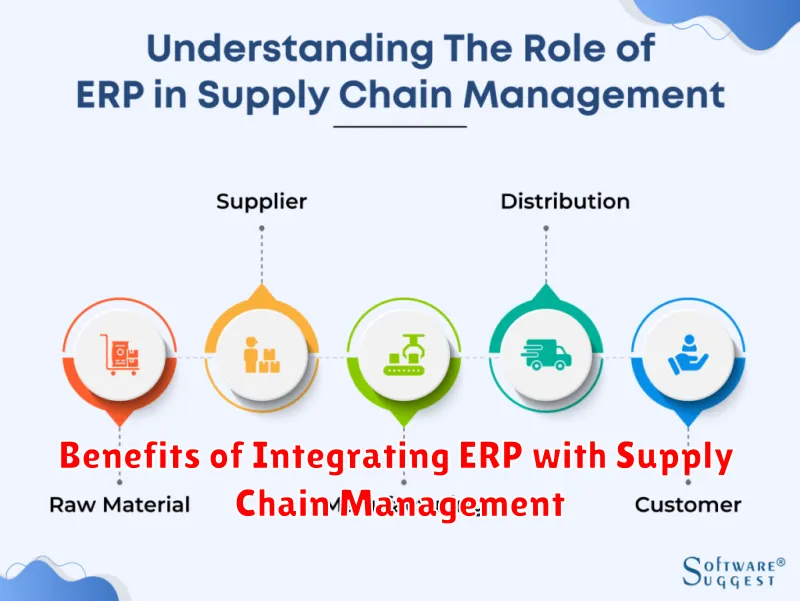
Integrating an Enterprise Resource Planning (ERP) system with Supply Chain Management (SCM) is a strategic decision that can bring significant benefits to organizations. By bridging the gap between these systems, companies can streamline their operations, optimize resource utilization, and enhance overall efficiency. The integration process enables data sharing and real-time visibility across different departments, resulting in improved decision-making and reduced errors.
Enhanced Visibility and Transparency
One of the key advantages of ERP-SCM integration is enhanced visibility and transparency throughout the supply chain. By connecting different systems, organizations can gain a real-time view of inventory levels, supplier performance, and customer demand. This real-time data enables proactive decision-making, ensuring that businesses have the right products in the right place at the right time.
Improved Inventory Management
ERP-SCM integration optimizes inventory management by providing accurate and up-to-date data on stock levels, demand forecasts, and supplier lead times. This allows businesses to reduce inventory carrying costs, minimize stockouts, and improve customer satisfaction. By automating inventory replenishment processes, organizations can streamline operations and free up resources for other strategic initiatives.
Streamlined Procurement
Integration facilitates seamless procurement processes, enabling companies to manage supplier relationships, negotiate better prices, and ensure timely delivery of goods. By connecting the ERP system’s purchasing module with the SCM platform, organizations can automate purchase orders, track deliveries, and manage vendor performance, leading to cost savings and improved efficiency.
Optimized Logistics and Transportation
ERP-SCM integration optimizes logistics and transportation by providing real-time visibility into shipment status, delivery schedules, and transportation costs. By connecting with transportation management systems (TMS), organizations can streamline route planning, optimize delivery schedules, and reduce transportation expenses. This integration also enables businesses to track shipments in real-time, providing improved customer service and reduced delivery delays.
Improved Customer Service
By integrating ERP and SCM, companies can enhance customer service by providing accurate order tracking, real-time delivery updates, and prompt responses to inquiries. This integrated approach enables businesses to meet customer expectations and build lasting relationships.
Conclusion
Integrating ERP with SCM is essential for businesses seeking to optimize their supply chain operations, reduce costs, improve efficiency, and enhance customer service. By seamlessly sharing data and automating processes across different departments, organizations can gain a competitive edge and achieve greater success in today’s dynamic business environment.